締結力の管理方法:トルク管理法について
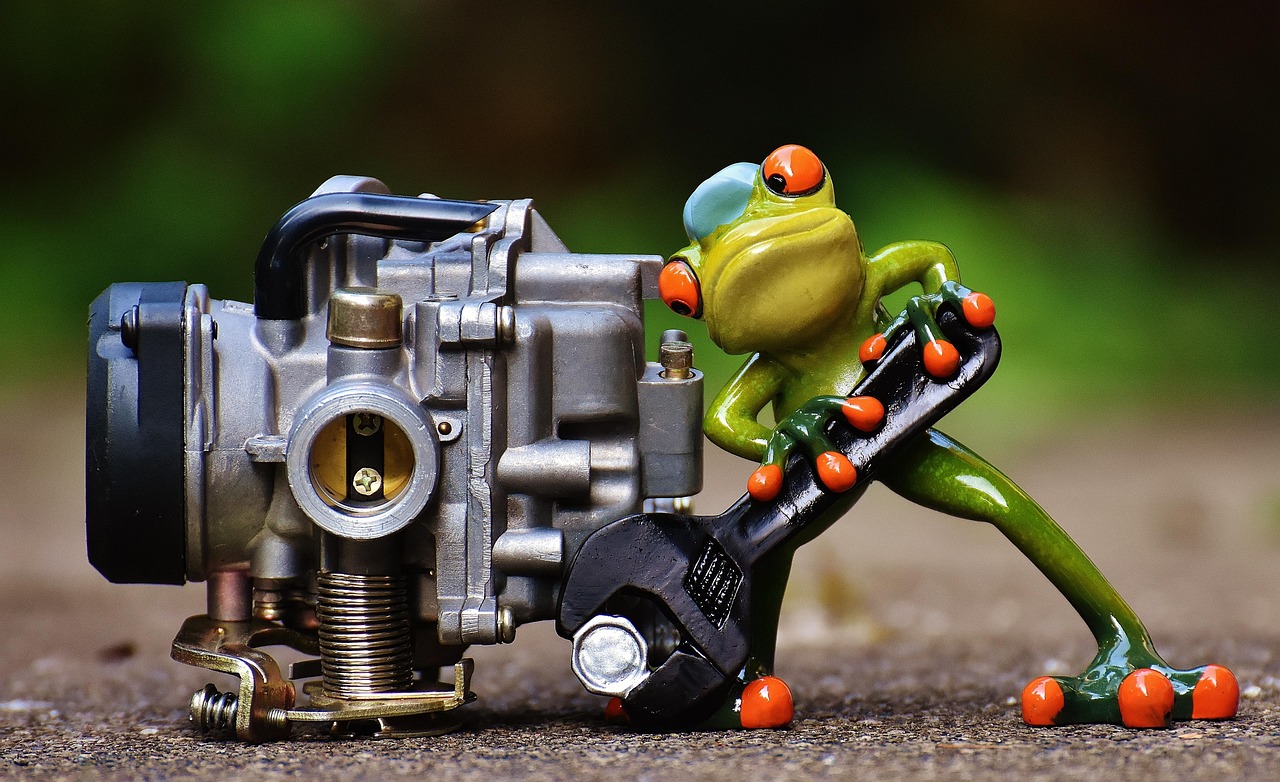
ボルト締結において、ボルトを確実に締め付けるために、どのような管理方法を思い浮かべるでしょうか?おそらく、多くの方が「トルク管理法」と答えるのではないでしょうか。
ねじは「回して締める」ものですから、その「回す力=トルク」で管理するという考え方は非常に直感的で分かりやすいですよね。実際、産業界で最も広く採用されているのが、このトルク管理法です。
現場にでは、トルクレンチを使わずに、いわゆる「手感」(ねじを回していくと嫌な感覚(塑性変形が始まる感覚)を覚えるが、その直前で止めるという熟練の感覚に頼った方法。)で締め付けている場面に出くわすこともあります。経験豊富な作業者にとっては有効な場合もありますが、定量的な管理とは言えず、締め付け力にばらつきが生じるリスクは避けられません。
今回は最もポピュラーな「トルク管理法」について、メリット、デメリットやその基本的な考え方から、具体的な方法、潜むリスク等を解説していきます。
1. トルク管理法とは? 基本を理解する
まず、「トルク管理法」がどのようなものか、基本からおさらいしましょう。
トルク管理法とは、その名の通り、ボルトを締め付ける際の「回す力(回転力)」、すなわち「トルク」の大きさを基準にして管理する方法です。トルクの単位は、国際単位系(SI)で N・m(ニュートンメートル) が用いられます。
- N(ニュートン): スパナやレンチといった工具にかける力の大きさを示します。
- m(メートル): ボルトの中心(回転軸)から力をかける点までの距離(腕の長さ)を示します。
トルク管理法では、設計段階や作業標準で「このボルトは〇〇 N・m で締め付けること」という具体的な目標トルク値を定めます。そして、作業者はトルクレンチと呼ばれる専用の工具を使用して、実際にボルトを締め付けます。
トルクレンチには様々な種類があります。
- プリセット型: あらかじめ設定したトルク値に達すると「カチッ」という音や感触で知らせるタイプ。最も一般的で、作業性に優れます。
- ダイヤル型・プレート型(弓型): 締め付けながら針や目盛りで現在のトルク値を確認できるタイプ。
- デジタル型: 締め付けトルクをデジタル表示し、設定トルクに達すると音や光で知らせるタイプ。精度が高く、データ記録が可能なものもあります。
これらのトルクレンチを用いることで、作業者の感覚に頼らず、定量的な数値に基づいて締め付け作業を行うことができます。これがトルク管理法の基本的な仕組みです。
2. トルク管理法のメリット:なぜ広く使われるのか?
トルク管理法がこれほどまでに普及している最大の理由は、その「簡便性」にあります。
最大のメリットは、トルクレンチさえあれば、比較的簡単に締め付け作業とその管理ができる点です。ボルト締結で本当に管理したいのは、ボルトに発生する「軸力(ボルトを引き伸ばす力、これによって部材が押さえつけられる)」なのですが、この軸力を直接測定するには、特殊なセンサー付きボルトや超音波測定器などが必要となり、コストも手間もかかります。
一方、トルク管理法では、軸力を発生させる入力値、つまり「締め付けトルク」を測定・管理すればよいため、非常に手軽です。トルクレンチは様々な種類が市販されており、比較的安価に入手できるものも多く、作業者への教育も比較的容易です。この導入の手軽さと運用しやすさが、トルク管理法がデファクトスタンダードとなっている大きな理由と言えるでしょう。
3. トルク管理法のデメリット:潜む根本的な課題
手軽で便利なトルク管理法ですが、実は大きなデメリット、あるいは根本的な課題を抱えています。それは
「締め付けトルクと、それによって発生する軸力は、必ずしも正確な比例関係にはない」
という点です。
言い換えると、いくらトルクレンチを使って目標トルク通りに精密に締め付けたつもりでも、毎回必ず同じ軸力が得られるとは限らない、ということです。これがトルク管理法の最大の弱点であり、時に予期せぬトラブルを引き起こす原因となります。
では、なぜトルクと軸力は単純な比例関係にならないのでしょうか?その理由は、締め付けトルクの多くが、軸力を発生させるためではなく、別の要因で消費されてしまうからです。一般的に、締め付けトルクのうち、
- 約 50% が 座面(ボルト頭部やナット下面)と被締結物との間の摩擦
- 約 40% が ねじ面の摩擦
によって消費され、実際に軸力(ボルトの伸び)に変換されるのは、わずか 10% 程度と言われています。
この「摩擦」という要素が非常に厄介で、様々な要因によって大きく変動するため、同じトルクをかけても軸力にばらつきが生じてしまうのです。次のセクションで、この「ばらつき」の原因となる要素を詳しく見ていきましょう。
4. 締め付けトルクの設定:標準トルク表の限界
トルク管理を行う上で、「締め付けトルク値」を決める必要があります。工具メーカーやMISUMIが提供する「標準締め付けトルク表」を見てみましょう。
- TONE(参考例): https://www.tonetool.co.jp/assets/pdf/support/links/torqwrench_figure.pdf
- MISUMI(参考例): https://jp.misumi-ec.com/tech-info/categories/technical_data/td01/a0198.html
これらの表を見ると、ボルトのサイズ(Mねじの呼び径)や強度区分(例: 4.8, 8.8, 10.9など)に応じて推奨トルク値が記載されています。しかし、よく見ると、同じサイズのボルトでも、メーカーによって推奨値が微妙に異なっていることに気づくはずです。
この違いは、主に以下の二つの理由によります。
- 想定しているトルク係数の違い: 前述の通り、トルクと軸力の関係は摩擦係数などに影響されます。この関係性をまとめて「トルク係数 (K)」という一つの係数で表現することがあります(T = K・d・Ff という式で表され、T:トルク, K:トルク係数, d:ねじの呼び径, Ff:軸力)。メーカー各社が標準トルク表を作成する際に、想定している摩擦係数(ねじ面、座面)や、その他の条件(締め付け速度など)が異なるため、トルク係数の値が変わり、結果として推奨トルク値に差が出ます。
- ボルト強度に対する考え方の違い: ボルトを締め付ける際、一般的にはボルトが降伏(永久変形)しない範囲で使用します。目標とする軸力を、ボルトの降伏点の何パーセントに設定するか(例えば60%なのか、70%なのか)、安全率をどう考えるかといった設計思想の違いが、推奨トルク値の違いとなって表れます。
ここで重要なのは、これらの標準トルク表は、あくまで一般的な条件下での「目安」であるということです。
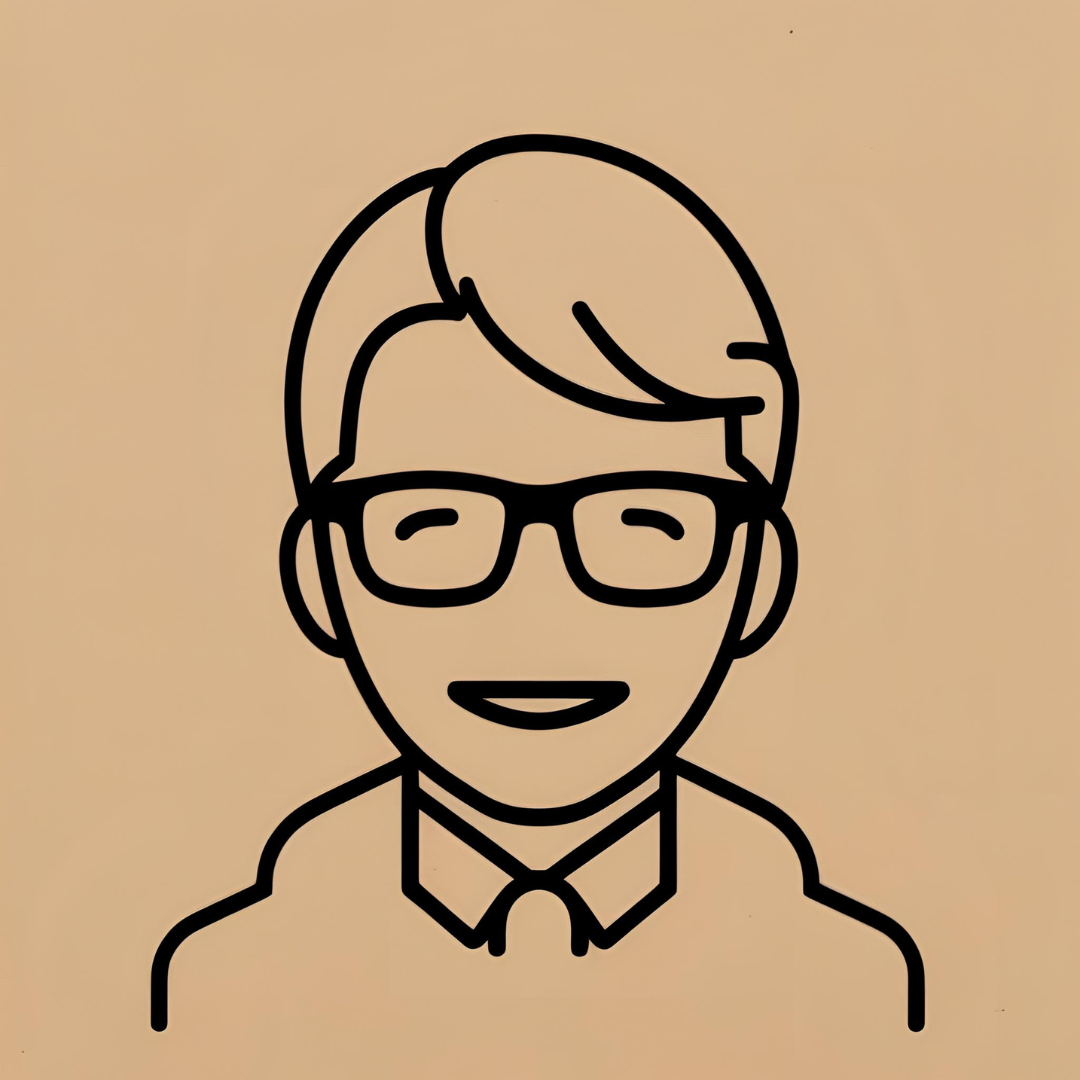
著者の感覚では、99%以上のケースでは上記の目安で大きな問題にはなりません。ですが、残りの1%以下で、問題を引き起こす可能性があります。
なぜなら、標準トルク表は、個別の締結条件における様々な要因を十分に考慮できていないからです。
※(正確に言うと考慮されています。ですが少し深く考慮してもらいたいと思ってあえてこう書きました。)
5. 標準トルク表での見落としがちなリスク要因
標準トルク表が万能ではない理由は、実際の締結が表の前提から外れるケースが多々あるためです。主な要因を挙げていきます。
要因1:外力の影響
ボルトを選定する際には、その締結部にかかるであろう「外力」(引張荷重、せん断荷重、曲げモーメント、振動、衝撃など)を考慮して、適切な太さ(呼び径)と強度区分のボルトを選びます。しかし、「いつもこの機械にはこのサイズのボルトを使っているから」といった慣習的な理由で、実際の外力条件を詳細に検討せずに選定してしまうケースはないでしょうか?
入力される外力によって、ボルトに必要な初期締結力(軸力)も変わってきます。また、外力の種類や大きさによっては、ねじの有効断面積だけでなく、ねじが相手材にねじ込まれている長さ(嵌合長)も重要になります。締結トルク値は、これらの外力を正確に把握した上で設計する必要があります。
要因2:被締結物の材質と座面状態
ボルトで締め付ける相手側の部品(被締結物)の材質も、トルク管理に影響を与えます。例えば、鋼鉄製のボルトで、アルミニウム合金や銅といった柔らかい材料を締め付ける場合を考えてみましょう。
これらの材料は、鋼鉄に比べて降伏点(塑性変形が始まる応力)が低いため、標準トルク表に基づいた高いトルクで締め付けると、ボルトの頭部やナットが接触する座面が陥没(へこむ)する可能性があります。これを「座面陥没」あるいは「座屈」と呼びます。
座屈すると、いくらトルクをかけてもボルトが空回りするような状態になったり、初期の軸力が徐々に低下して緩みの原因になったりします。これを防ぐためには、
- 座金(ワッシャー)を入れる
- ボルト頭部やナット下面の接触面積が大きいフランジ付きボルト・ナットを使用する
等で座面にかかる圧力(面圧)を分散させる必要があります。しかし、ワッシャーを入れたり、フランジ形状が変わったりすると、座面の摩擦係数が変化するため、トルク係数が変わり、結果として同じトルクでも発生する軸力が変わってしまうことに注意が必要です。
要因3:摩擦係数(トルク管理の最大の敵!)
これが、トルク管理において最もコントロールが難しく、軸力ばらつきの最大の原因となる要素です。前述の通り、締め付けトルクの大部分(約90%)は摩擦によって消費されますが、この摩擦係数が非常に不安定で、様々な要因によって大きく変動します。
- 表面粗さ(面粗度): ねじ山や座面の表面の面粗度は摩擦係数に直接影響します。例えば図面で加工面粗度 Ra6.3と指示されているとします。これは「平均粗さが6.3μm以下」という意味であり、1μmでも5μmでも問題ないのです。実際の生産現場では、刃具の摩耗や折損で生産を重ねるにつれて面粗度が荒くなる傾向があります。また、なぜか同条件、新品刃具でもなぜか条件が出ない(ばらつく)といったこともあります。さらに、めっきやコーティングなどの表面処理の有無や種類、膜厚のばらつきも摩擦係数を変動させます。こういったばらつきがあるので、一般的には図面には最悪値を書きます。なので、同じ図面でも表面粗さは非常にきれいであったり、図面値ギリギリであったりするのです。
- めねじ側の状態: おねじ(ボルト)だけでなく、めねじ(ナットやタップ穴)の状態も重要です。ねじ山を削って作る「切削タップ」と、材料を盛り上げて成形する「転造タップ」では、ねじ面の状態が異なり、摩擦係数も変わってきます。タップの摩耗や損傷、めねじ側の材質や表面処理も影響します。
- 潤滑状態: 意図的に油やグリス、焼き付き防止剤などを塗布するかどうかで、摩擦係数は劇的に変化します。塗布する潤滑剤の種類や量によっても効果は異なります。また、意図せず部品に付着している油分(防錆油や切削油の残りなど)や、ゴミ、切粉などの異物の存在も、摩擦係数を不安定にする要因です。乾燥した状態か、潤滑された状態かで、トルク係数は2倍以上変化することも珍しくありません。
- 締め付け速度: 手締めでゆっくり締め付ける場合と、電動工具(ナットランナーなど)で高速に締め付ける場合とでは、摩擦の状態(静摩擦係数と動摩擦係数のどちらが支配的か)が異なります。一般的に、高速かつ一定速度で締め付けるナットランナでは動摩擦係数支配的になり、摩擦係数は低くなる傾向があります。一方、手締めのように速度が不均一だと、静止摩擦係数と動摩擦係数を行ったり来たりして摩擦係数が安定せず、軸力のばらつきにつながりやすくなります。
- その他: 温度や湿度といった環境条件、ボルトやナットの再利用(なじみによる摩擦変化や、ねじ山の損傷)、ボルトやナットの精度(等級)なども、摩擦係数に影響を与えます。
このように、摩擦係数は極めて多くの要因に影響され、非常にばらつきやすいのです。
6. 軸力ばらつきが引き起こすリスク
摩擦係数がこれほど不安定であるということは、トルク管理法で締め付けた場合に、発生する軸力も大きくばらつく可能性があることを意味します。
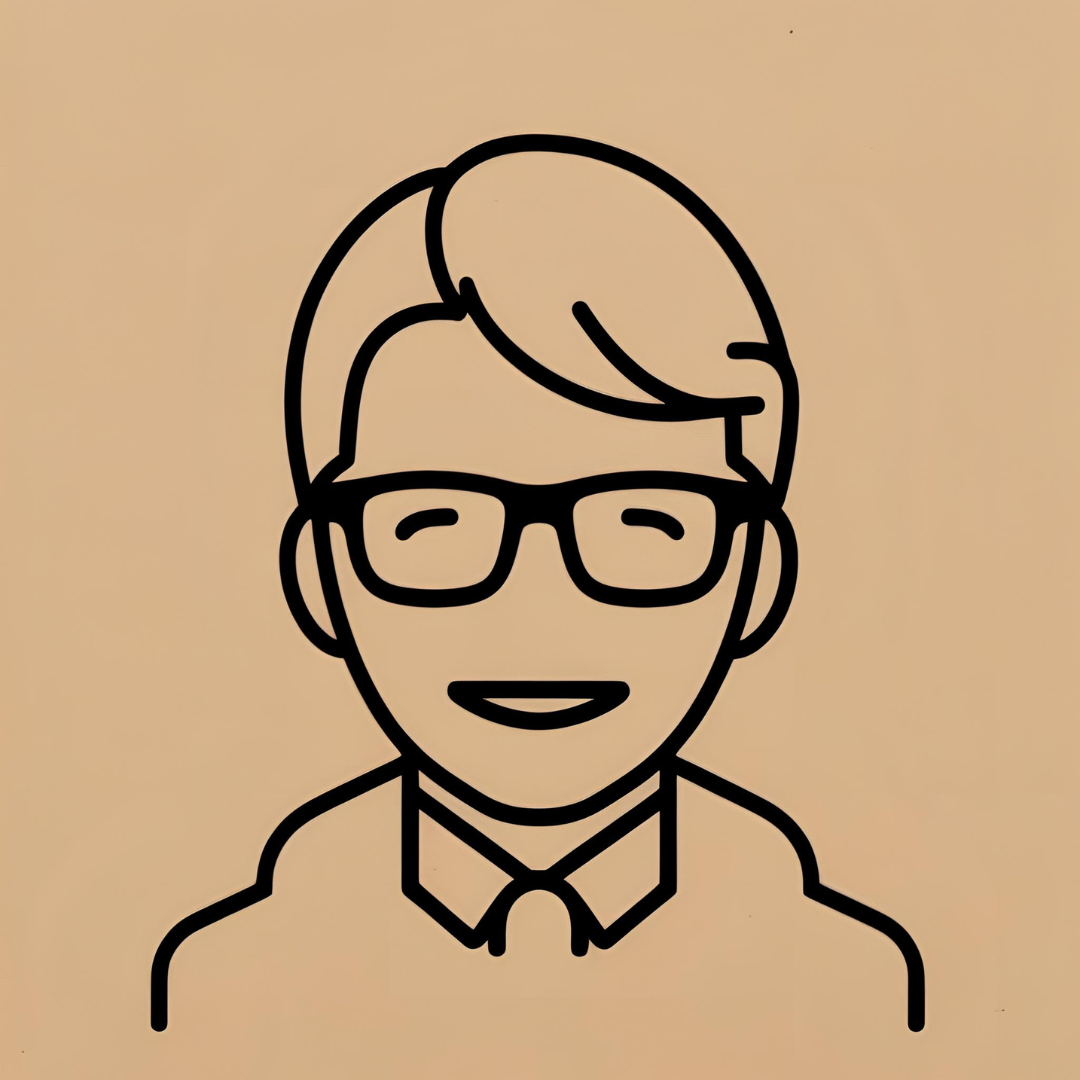
著者の経験では、量産品を用いて全く同じ部品構成、同じ目標トルクで締め付けたにもかかわらず、実際に発生した軸力が倍以上も異なったというケースがありました。
【軸力が想定より高すぎる場合のリスク】
- ボルトの塑性変形・降伏: ボルトが必要以上に引き伸ばされ、元に戻らない永久変形を起こる。
- ボルトの破断(ねじ切れ): 締め付け中、あるいは使用中にボルトが限界を超えて破断する。
- 被締結物の損傷: 座面が陥没したり、被締結物自体が変形・破損する。
【軸力が想定より低すぎる場合のリスク】
- 初期緩み: 部品同士のなじみやガスケットのへたりなどにより、初期の軸力が低下する。
- 進行性の緩み: 振動や衝撃、温度変化による部材の伸縮などによって、ボルトが回転して緩みする。
- 部品間のずれ(相対運動): 締結力が不足し、部品同士が微小にずれ動くことで、摩耗(フレッティング摩耗)や異音が発生し、最終的に軸力が落ちる。
- シール性の低下: ガスケットやOリングなどを用いたシール部で、十分な面圧が得られず、液体や気体が漏れる。
- 疲労破壊: 締結力が不足していると、ボルトにかかる変動荷重の振幅が大きくなり、疲労破壊に至る。
トルク管理法は手軽である反面、これらのリスクがある事を理解しておく必要があります。設計時点でロバスト性の高い締結設計をする必要があるのです。
7. まとめ:トルク管理法を知り最適な締結へ
今回は、ボルト締結管理の最も基本的な方法である「トルク管理法」について、その仕組みからメリット、そして特に重要なデメリットとリスクについて詳しく解説しました。
トルク管理法の要点
- メリット: トルクレンチがあれば比較的簡単に実施でき、広く普及している。
- デメリット: 締め付けトルクと発生軸力の関係は、摩擦係数の大きなばらつきにより、必ずしも比例しない。
- リスク: 軸力が想定より高すぎたり低すぎたりすることで、ボルトの破損、緩み、被締結物の損傷、疲労破壊など、様々な不具合を引き起こす可能性がある。
標準締め付けトルク表はあくまで目安であり、実際の締結においては、外力、被締結物の材質、座面状態、そして何よりもコントロールが難しい摩擦係数といった多くの要因を考慮する必要があります。
「たかがねじ、されどねじ」です。もし、あなたの現場でねじの緩みや破損といった問題が発生している場合、単に「トルクが足りなかった」「締め方が悪かった」と結論付ける前に、今回解説したような要因、特に摩擦係数に影響を与える要素(潤滑、表面状態、工具、速度など)が管理されているか、またはその管理だけで十分か(=トルク管理で成立する締結なのか)といった視点で見直してみてはいかがでしょうか。
トルク管理法では十分に軸力を管理できない場合、回転角法を導入する、直接軸力測定する等も検討すべきかもしれません。これらの方法については別ページで解説しますね。
ボルト締結は奥が深いです。より安全で確実なモノづくりの一助となれば幸いです。