ボルトの強度区分
適切な選定で安全な設計を実現機械設計において、使用するボルト(ねじ)の強度を正しく選定することは、製品の安全性や信頼性を確保する上で非常に重要です。強度不足のボルトを使用すれば、荷重に耐えきれず破損事故につながる可能性があります。逆に、必要以上に高強度なボルトを選んでしまうと、コストの無駄遣いになってしまいます。
そこで役立つのが「強度区分」という指標です。強度区分は、ボルトの機械的な強さを示すもので、適切なボルト選定のガイドラインとなります。
この記事では、ボルトの強度区分について詳しく解説し、設計においてどのようにボルトを選定すればよいかを分かりやすく説明します。
強度区分とは? – ボルトの強さを知るための基準
ボルトの強度区分とは、そのボルトが持つ引張強度や降伏強度といった機械的特性に基づいて、ボルトを分類するための基準です。JIS(日本産業規格)などで規格化されており、設計者はこの区分を目安に、特定の荷重条件や使用環境に適したボルトを選ぶことができます。
強度区分は、通常「4.8」や「8.8」、「10.9」のように、小数点を含む2つの数字で表記されます。鋼製のボルトでは、一般的に以下の10段階に区分されています。
- 3.6
- 4.6
- 4.8
- 5.6
- 5.8
- 6.8
- 8.8
- 9.8
- 10.9
- 12.9
この2つの数字には、それぞれ意味があります。
- 最初の数字 (例: 8.8 の「8」)
- ボルトの最小引張強さの100分の1を表します。単位は N/mm² です。
- 例:「8.8」の場合、最小引張強さは 8×100=800 N/mm² となります。
- 2つ目の数字 (例: 8.8 の「8」)
- 降伏強度と引張強度の比率(降伏比)を10倍した値を示します。
- 例:「8.8」の場合、降伏強度は引張強度の 8×10=80% 、つまり 800×0.8=640 N/mm² となります。
「引張強度」と「降伏強度」 – 設計で重要な2つの指標
強度区分を理解する上で欠かせないのが、「引張強度」と「降伏強度」です。
- 引張強度 (Tensile Strength)
- ボルトが破断するまでに耐えられる最大の引張応力(単位面積あたりの力)を指します。ボルトを引っ張っていくと、最終的にちぎれてしまいますが、その限界点が引張強度です。
- 降伏強度 (Yield Strength)
- ボルトが永久変形(塑性変形)を起こし始める応力を指します。この強度を超えると、力を取り除いてもボルトは元の形状に戻らなくなります。引張強度に達する前に、まず降伏が起こります。
設計への影響:なぜ降伏強度が重要なのか?
設計においては、ボルトが破断しないことはもちろん、永久変形しないことも非常に重要です。ボルトが降伏してしまうと、締結力が低下したり、部品の位置がずれたりして、機械の機能不全や事故につながる可能性があります。
そのため、安全な設計を行う上では、ボルトにかかる応力が降伏強度を超えないようにすることが基本となります。引張強度はボルトが耐えられる限界の強さを示しますが、実用的な設計基準としては降伏強度がより重視されるのです。
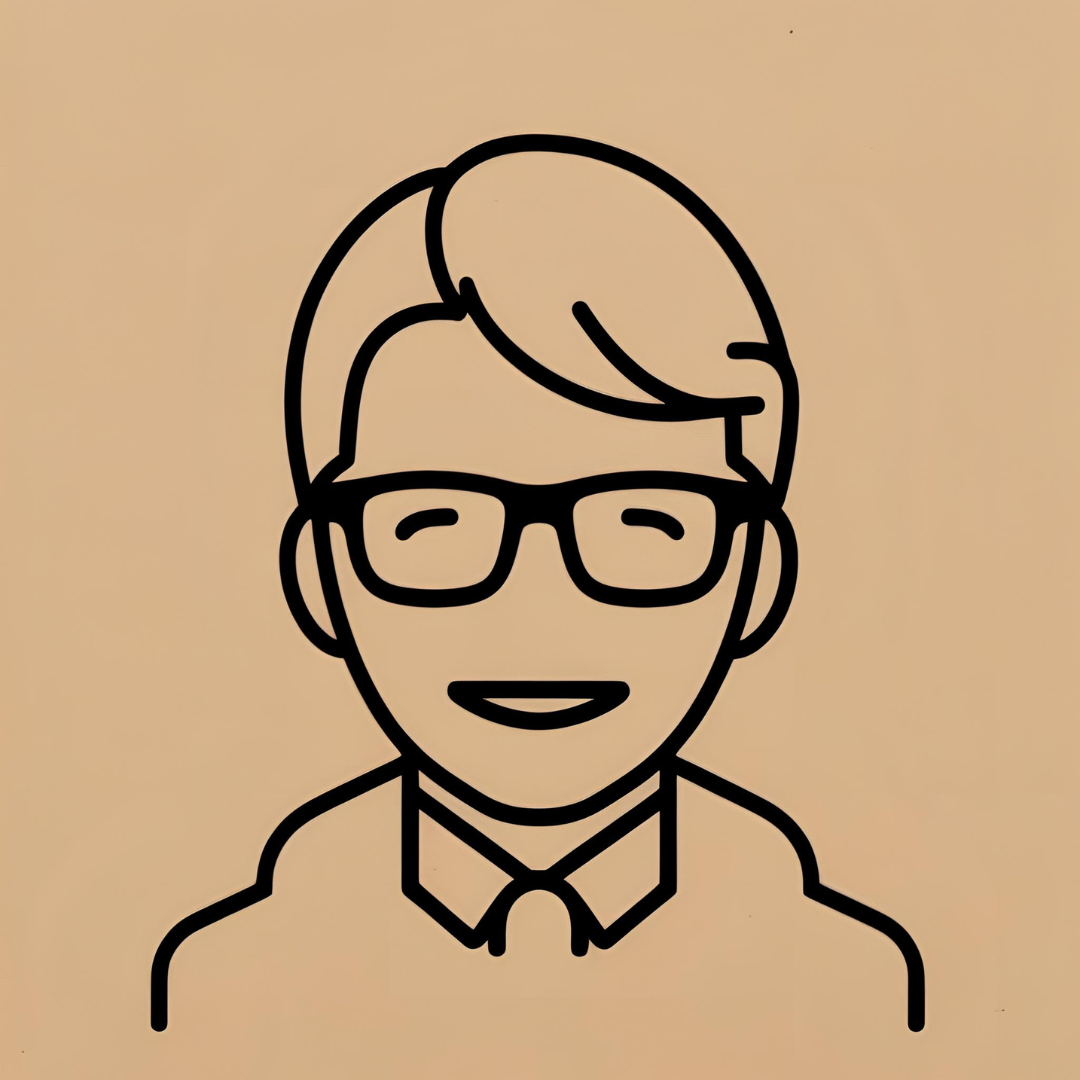
実は、わざと降伏点を超えて締結する手法があります。塑性域回転締付法などと呼ばれる手法です。
この手法は、管理された降伏点と、外力(熱膨張力含む)、被締結物のばね定数がすべて設計範囲に管理できる場合に使われる設計難易度の高いもので、エンジンブロックの締付などに使われます。
今後、別途解説しますね
鋼鉄製ボルトの強度区分と特徴
機械設計で最も一般的に使用されるのが鋼鉄製のボルトです。主な強度区分とその特性を見ていきましょう。
- 強度区分 4.8: 比較的弱いボルトで、大きな力がかからない部分や、軽量な構造物などに使われます。
- 強度区分 8.8: 機械設計において最も標準的に使われる強度区分です。一般的な機械部品の締結に適しており、コストと強度のバランスが良いのが特徴です。材質としては、S45Cなどの炭素鋼が用いられることがあります。
- 強度区分 10.9: 高い強度が必要な箇所に使用されます。自動車のエンジンや足回り、産業機械など、安全性や耐久性が特に求められる部分に適しています。合金鋼(例:SCM435 クロムモリブデン鋼)に焼入れ焼戻しといった熱処理を施して製造されます。
- 強度区分 12.9: 非常に高い強度を持つボルトです。極めて大きな引張力がかかる特殊な用途、例えば重機のアーム部分や航空機の重要部品などに用いられます。10.9と同様に、合金鋼への熱処理によって高い強度が得られます。
さらに高強度なボルトと注意点:水素脆性
JIS規格にはありませんが、メーカーによっては「14.9」や「16.9」といった、12.9を超えるさらに高強度なボルトも存在します。これらは主に、軽量化と高性能化を極限まで追求するレーシングカーなどの特殊な分野で利用されることがあります。
ただし、一般的には12.9までの強度があれば、ボルト径を太くすることで必要な強度を確保できる場合が多いです。これは、ボルト自体の強度を上げても、相手材(めねじ)の強度や座面の耐力が限界となり、高強度ボルトのメリットを活かしきれないケースがあるためです。
また、10.9以上の高強度ボルトを使用する際には、「水素脆性(すいそぜいせい)」または「遅れ破壊」と呼ばれる現象に注意が必要です。
水素脆性とは?
水素脆性とは、金属材料、特に高強度鋼が水素を吸収することで、延性(粘り強さ)が低下し、脆くなる現象です。通常よりも低い応力で、ある程度の時間が経過した後に突然破壊(遅れ破壊)することがあります。
- 原因:
- 水素の吸蔵: 製造工程(特にめっき処理)や使用環境(腐食環境)で発生した水素が、金属内部に侵入・蓄積します。
- 応力の存在: 水素が吸蔵された状態で引張応力がかかると、水素が応力集中部に集まり、原子間の結合を弱めて亀裂の発生・進展を助長します。
- 発生しやすい条件:
- 高強度鋼: 強度が高いほど水素脆性の感受性が高まります。一般的に強度区分10.9以上、特に12.9で注意が必要です。
- 腐食環境: 湿度の高い場所や酸性雨など、腐食によって水素が発生しやすい環境。
- 高い応力: ボルトに高い引張応力がかかっている状態。
- めっき処理: 電気めっきなどの処理工程で水素が発生し、吸蔵されることがあります。
鉄製のボルトは、錆防止や外観向上のためにめっき処理が施されることが多いですが、「高強度」「高応力」「めっき処理」という条件が揃うと、水素脆性による破壊リスクが高まります。
水素脆性の対策
- めっき処理をしない: 油中など、常に潤滑されている環境で使用する場合は、めっきなしのボルト(黒染めなど)を使用するのが有効です。
- 非電解めっきや代替表面処理を用いる: めっき処理が必要な場合は、水素を発生させにくい非電解めっき(カニゼンめっきなど)や、水素脆性のリスクが低いとされる特殊な表面処理(例:ジオメット処理、デルタプロテクトなど)を検討します。
- ベーキング処理: めっき後に行われる熱処理(ベーキング)で、吸蔵された水素を放出させる対策もありますが、完全ではありません。10.9ボルト等で用いられます。
注意点: 表面処理の種類によってボルトとナット間の摩擦係数が変わります。締結トルクから軸力を正確に計算するためには、使用する表面処理に適した摩擦係数を用いる必要があります。
ステンレス製ボルトの強度区分
ステンレス鋼製のボルトも広く使われています。最大のメリットは優れた耐食性ですが、一般的な鋼鉄製ボルトと比較すると強度は低めになる傾向があります。
ステンレスボルトの強度区分は、主に材質を示す「A2」や「A4」といった記号と、引張強度を示す数字(例:「70」は引張強度700 N/mm²)を組み合わせて表現されます。
- A2: 一般的なステンレス鋼(SUS304系)。耐食性に優れ、広く使われます。
- A4: A2にモリブデンを添加したステンレス鋼(SUS316系)。A2よりもさらに耐食性が高く、特に塩化物イオンに対する耐性が求められる沿岸部や化学薬品を扱う環境に適しています。
鋼鉄製ボルト vs ステンレス製ボルト – 用途に応じた選択
どちらの材質のボルトを選ぶかは、要求される強度、使用環境、コストなどを総合的に判断する必要があります。
強度区分の選定ポイント – 後悔しないボルト選びのために
適切な強度区分のボルトを選定するために、以下の点を考慮しましょう。
- 荷重条件の確認: ボルトにかかる最大の力(引張荷重、せん断荷重など)を計算または予測します。そして、その荷重に対して十分な安全余裕を持てるよう、降伏強度を基準に強度区分を選定します。安全率は、用途や重要度に応じて適切に設定する必要があります。
- 使用環境の考慮:
- 温度: 高温環境では、高温強度に優れた材質や強度区分の選定が必要です。
- 腐食: 湿気、薬品、塩分などの腐食環境では、ステンレス製ボルトや適切な表面処理が施された鋼鉄製ボルトを選びます。
- 振動・衝撃: 振動や衝撃が加わる箇所では、疲労強度が高いボルトや、緩み対策が施されたボルトを検討します。
- ねじのサイズ(呼び径): 同じ強度区分でも、ボルトの径が太くなるほど耐えられる荷重は大きくなります。必要な強度を満たす最小限のサイズを選ぶことで、コストや重量を最適化できます。
- 材料と熱処理: 強度区分は、ボルトの材質とその熱処理方法によって決まります。要求される強度区分を満たす材質(炭素鋼、合金鋼など)が使われているかを確認します。特に高強度ボルトでは、SCM435などの合金鋼が熱処理されて使われることが一般的です。
まとめ – 適切な強度区分で安全・安心な設計を
ボルトの強度区分は、機械設計における縁の下の力持ちでありながら、その選定は製品全体の安全性と性能を左右する重要な要素です。
- 強度区分は、ボルトの引張強度と降伏強度を示す指標。
- 設計では、降伏強度を超えないように選定するのが基本。
- 鋼鉄製は強度に優れ、ステンレス製は耐食性に優れる。
- 高強度ボルト (10.9以上) は、水素脆性に注意が必要。
- 荷重、環境、サイズ、材質を考慮して最適な強度区分を選ぶ。
単に「ボルトで締めれば良い」と考えるのではなく、設計要件をしっかりと把握し、必要な強度を持つボルトを選定することが不可欠です。強度計算や締結計算をきちんと行い、適切な強度区分のボルトを使用することで、安全で信頼性の高い製品づくりを目指しましょう。