歯車のキホン。モジュール、歯型、圧力角、転移量を解説
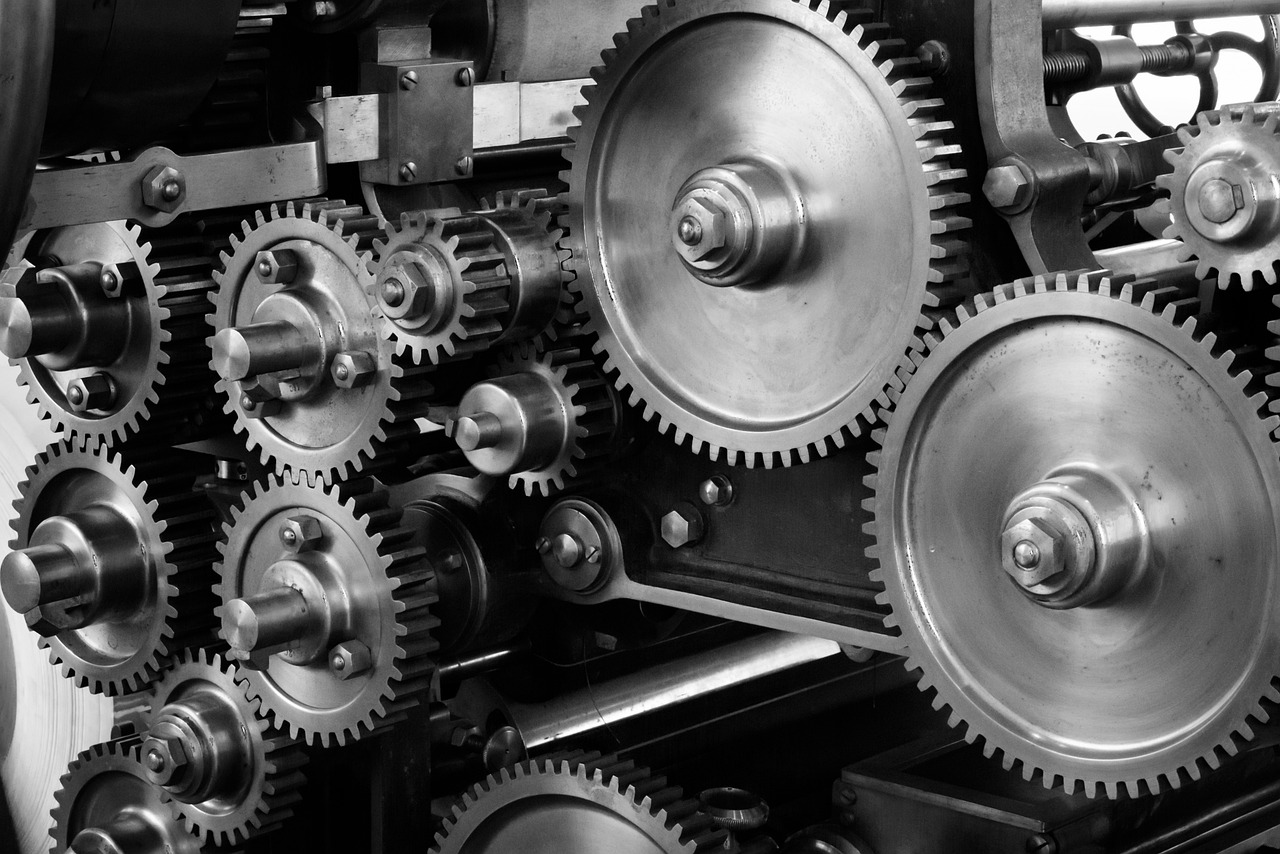
1. はじめに
私たちの身の回りにある自動車、時計、工場の機械など、多くのものが歯車(ギア)の力で動いています。カタカタと音を立てて回るものもあれば、静かに、しかし確実に力を伝えているものもあります。これらの歯車が、なぜうまく噛み合って動くことができるのでしょうか?
その秘密は、歯車の設計に関わるいくつかの基本的な「ルール」や「パラメータ」にあります。今回は、その中でも特に重要な4つのキーワード、「モジュール(Module)」、「歯型(Tooth Profile)」、「圧力角(Pressure Angle)」、そして「転移量(Profile Shift)」について、初心者の方にも分かりやすく、やさしく解説していきます。
この記事を読めば、歯車がどのように設計され、なぜ異なる歯車同士が噛み合うことができるのか、その基本的な仕組みが理解できるはずです。複雑な数式は極力避け、それぞれの用語が何を意味し、なぜ重要なのか、その本質を掴んでいきましょう。
2. 歯車の「大きさ」を決める最重要要素:モジュール
モジュールとは?
歯車の世界に足を踏み入れると、まず最初に出会うのが「モジュール(m)」という言葉でしょう。これは一体何なのでしょうか?簡単に言うと、モジュールは歯車の「歯の大きさ」を表す基本的な数値です。歯のサイズを示す一種の「コード」だと考えてください。
もっとイメージしやすくするために、一旦、歯の「形(歯型)」や歯を作る際の「位置調整(転移)」、そして力の伝わる「角度(圧力角)」は考えないことにします。これらを「普通の形(並歯)」で「標準の角度(例えば20°)」、「調整なし(転移ゼロ)」に固定した場合、モジュールが大きくなれば歯も大きくなり、モジュールが小さくなれば歯も小さくなります。まさに、歯のサイズそのものを表す指標なのです。
モジュールと歯の寸法
では、具体的にモジュールが変わると、歯の大きさはどれくらい変わるのでしょうか?ここで一つ、具体的な例を見てみましょう。もしモジュール(m)が 1 だとすると、その歯車の歯の頂上から谷底までの長さ、つまり「全歯たけ」は 2.25mm になります。そして、もしモジュールが 2 になれば、全歯たけはその2倍の 4.5mm となります。
また、歯車のピッチもモジュールによって決まります。ピッチ(p)とは、隣り合う歯の対応する点(例えば、歯の中心線)間の距離をピッチ円(歯車が噛み合う際の基準となる仮想的な円)の円周上で測ったものです。このピッチは、p=π×m という関係式で表されます。つまり、モジュールが大きくなれば、歯の間隔も広がるのです。
このように、モジュールの値と歯の寸法(高さ、厚み、ピッチなど)は直接的な比例関係にあります。「なぜモジュール 1 で全歯たけがちょうど 2.25mm なの?」と疑問に思うかもしれません。この「2.25」という数字は、歯車の設計における世界共通の取り決め(歯先の高さ=1×m、歯元の深さ=1.25×m、合計 2.25×m というのが一般的な基準)から来ています 1。今は詳細な計算式を覚える必要はありません。「モジュールという基準値があって、それに比例して歯の各部寸法が決まる」という点、特にその標準化された比例関係が重要だと覚えておきましょう。
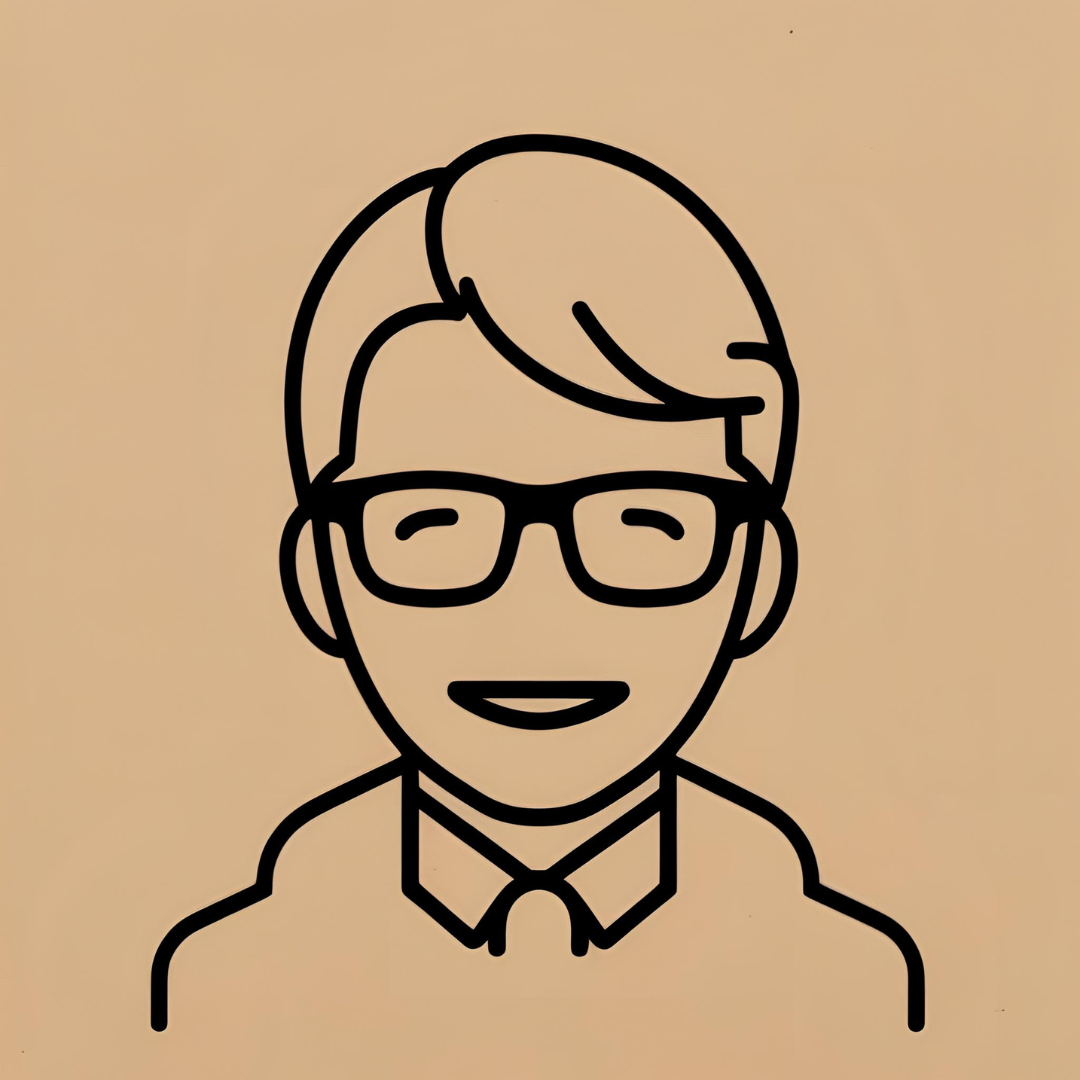
世界中で共通と言ったけど、アメリカやイギリスはポンド・フィート法をよく使っています。よみかえる係数を加えねばならないので要注意です!!
ただし、注意点があります。モジュールが変わると、歯の高さだけでなく、歯の厚みや、隣り合う歯との間の距離(ピッチ)など、歯全体の形状が相似形を保ったまま拡大・縮小します。つまり、モジュールを大きくすると、単に背が高い歯になるのではなく、全体的にがっしりとした大きな歯になるのです。この「相似形での変化」という性質が、後で説明する「歯型」や「転移量」といった他のパラメータが必要になる理由の一つにも繋がってきます。
世界共通のルール:規格の重要性
このモジュールという考え方の素晴らしい点は、世界中で共通の規格として定められていることです 。日本のJIS規格でも、国際的なISO規格でも、モジュールの定義は基本的に同じです 。これにより、町工場で作られた歯車も、大企業の最新工場で作られた歯車も、同じモジュールであれば基本的な歯のサイズが同じになります。
なぜこのような規格が重要なのでしょうか?それにはいくつかの大きな理由があります。
- 互換性(Interchangeability): 同じモジュール(そして後述する歯型や圧力角なども)で作られた歯車であれば、異なるメーカーが作ったものであっても基本的には噛み合わせることができます。これは機械の修理や部品調達において非常に重要です。
- 設計と製造の簡略化: もしモジュールが自由な値を取れたら、設計や製造に必要な工具の種類は無限に増えてしまいます。規格によって使用するモジュールの値が絞られることで、設計計算が楽になり、製造に必要な工具や在庫管理も効率化され、コスト削減に繋がります。
- グローバルな取引: 日本で作られた機械の補修部品として、海外で作られた同じモジュールの歯車を使う、といったことが可能になります。これは、国際的な機械・部品の貿易を円滑にする上で不可欠な要素です。
このように、モジュールの標準化は、歯車を使う全ての産業にとって、計り知れない恩恵をもたらしているのです。
モジュールの選び方:標準モジュール
では、歯車を設計する際、モジュールはどんな値でも自由に選べるのでしょうか? 答えは「いいえ」です。モジュールには、「標準モジュール」として定められた値があり、通常はこの中から選ぶ必要があります 。勝手に「モジュール 1.3」のような値を使うことは、特別な理由がない限り避けられます。
標準モジュールには、よく使われる「第一系列(Series I)」と、第一系列では都合が悪い場合に用いられる「第二系列(Series II)」があります。まずは第一系列から選び、それで目的を達成できない場合に第二系列を検討するのが一般的です。これらの値は、JIS B 1701-1 や ISO 54 といった規格で定められており、一般的には 0.1 から 50 程度の範囲で具体的な数値がリストアップされています。
以下に、よく使われる標準モジュール(第一系列と第二系列の一部)の例を示します。
表1:標準モジュール(JIS B 1701-1:2016 より抜粋)
系列 | 標準モジュール (m) |
第一系列 | 0.1, 0.2, 0.3, 0.4, 0.5, 0.6, 0.8, 1, 1.25, 1.5, 2, 2.5, 3, 4, 5, 6, 8, 10, 12, 16, 20, 25, 32, 40, 50 |
第二系列 | 0.15, 0.25, 0.35, 0.45, 0.55, 0.7, 0.9, 1.125, 1.375, 1.75, 2.25, 2.75, 3.5, 4.5, 5.5, 7, 9, 11, 14, 18, 22, 28, 36, 45 |
(太字は特に一般的に使われることが多い値の例)
このように決められた値から選ぶことで、前述した標準化のメリット(互換性、製造の容易さなど)が最大限に活かされるわけです。
まとめ:モジュールが同じなら噛み合える(かも)
モジュールについて、ご理解いただけたでしょうか? 最も重要なポイントは、「モジュールは歯の大きさを決める基本指標であり、同じモジュールの歯車同士は噛み合うための基本的な条件を満たしている」ということです。相手の歯車の歯数が多くても少なくても、モジュールが同じであれば、基本的な歯のサイズが適合するため、噛み合うための第一条件をクリアしていると言えます。
ただし、これだけでは十分ではありません。実際に歯車が正しく噛み合って力を伝えるためには、後述する「歯型」や「圧力角」といった他の重要な要素も一致している必要があります。モジュールは、いわば歯車が噛み合うための「入場券」のようなものだと考えましょう。
3. 歯の「形」と性能:歯型
モジュールが歯の「全体的な大きさ」を決める基本パラメータであることは分かりました。次に注目するのは、歯の「形」、特にその高さの比率に関わる「歯型(Tooth Profile)」です。
歯型とは?並歯・高歯・低歯
歯型とは、文字通り歯の形状のタイプを指します。モジュールが同じでも、歯型が異なると歯の高さ(正確には、歯たけ=歯先円直径と歯底円直径の差の半分)が変わってきます。一般的に使われる歯型には、主に以下の3種類があります。
- 並歯(なみば、Standard Tooth): 最も標準的な歯型です。特別な指定がない場合は、通常この歯型を指します。歯たけはモジュールの 2.25 倍(全歯たけ = 2.25m)が基準となります。
- 高歯(たかば、High Tooth / Full Depth): 並歯よりも歯たけが高い歯型です。例えば、全歯たけが 2.5m や 3.0m など、基準より高く設定されます。
- 低歯(ひくば、Stub Tooth): 並歯よりも歯たけが低い歯型です。例えば、全歯たけが 2.0m や 1.8m など、基準より低く設定されます。
なぜ歯型が違うのか?
モジュールが決まれば歯の大きさ(高さも含む)が決まるのに、なぜわざわざ「高歯」や「低歯」といった異なる歯型が必要なのでしょうか?その理由は、先ほど触れた「モジュールは歯の形状を相似形で拡大・縮小する」という性質にあります。
モジュールを変更すると、歯の高さだけでなく、歯の間隔(ピッチ)も変わってしまいます。しかし、設計によっては「歯の間隔(ピッチ)は変えずに、歯の高さだけを変えたい」あるいは「歯の強度を上げたい(=歯を低く、太くしたい)」という要求が出てくることがあります。
例えば、同じモジュール(つまり同じピッチ)のままで、歯の強度を上げたいと考えたとします。もしモジュールだけで調整しようとすると、モジュールを小さくすることになり、ピッチも変わってしまいます。しかし、「低歯」という歯型を選べば、モジュール(ピッチ)を変えずに歯たけだけを低くすることができ、結果として歯元が相対的に太くなり、強度を高めることが可能になります。逆に、より滑らかなかみ合いを求めて「高歯」を選ぶこともあります。
このように、歯型は、モジュールによって決まる基本的な寸法(特にピッチ)を維持しながら、歯の高さに関連する性能(強度や滑らかさ)を調整するための重要な設計パラメータなのです。歯型は、モジュールによる比例的なスケーリングから「歯たけ」という要素をある程度独立させて調整する手段を提供します。
歯型による性能の違い:強度と静音性
では、歯型が違うと、具体的にどのような性能差が出るのでしょうか? 主な違いは「強度」と「静音性(かみ合いの滑らかさ)」に現れます。
- 低歯(Stub Tooth):
- メリット: 歯たけが低いということは、同じモジュール(同じピッチ円直径)であれば、歯の根元部分が相対的に太くなります。テコの原理を考えても分かるように、根元が太い方が曲げに対する強度は高くなります。したがって、低歯は強度的に有利です。大きな力を伝える必要がある場合や、衝撃荷重がかかるような用途で選ばれることがあります。
- デメリット: 歯が低い分、後述する「かみ合い率」が低くなる傾向があり、滑らかさや静音性の点では並歯や高歯に劣ることがあります。
- 高歯(High Tooth):
- メリット: 歯たけが高いと、「かみ合い率(Contact Ratio)」を高めることができます 。
- かみ合い率とは?: かみ合い率とは、歯車が回転している間に、常に何組の歯が同時にかみ合っているかを示す平均の値です。例えば、かみ合い率が 1.5 であれば、常に1組の歯が完全にかみ合っており、それに加えて半分の時間、もう1組の歯がかみ合っている、という状態を意味します。
- かみ合い率が高いとどうなる?: 同時にかみ合っている歯の数が増えると、力が分散され、一つの歯にかかる負担が減ります。また、歯と歯が接触したり離れたりする際の衝撃が緩和され、歯車同士の相対的なガタつき(バックラッシの影響などによる微小な動き)も抑えられます。これにより、運転が滑らかになり、騒音が低減されます 。つまり、高歯は静音性や滑らかな回転に有利です。
- デメリット: 歯が高く細長くなるため、同じ材質であれば曲げ強度は低歯や並歯に比べて低下します 。
- メリット: 歯たけが高いと、「かみ合い率(Contact Ratio)」を高めることができます 。
- 並歯(Standard Tooth):
- 強度と静音性のバランスが取れた、最も一般的な歯型です。
このように、歯型の選択は、「強度を優先するか、静音性・滑らかさを優先するか」というトレードオフの関係にあります。設計者は、その歯車が使われる機械の目的や要求性能(例えば、大きなトルクを伝える建設機械のギアなら強度重視、静粛性が求められる乗用車のトランスミッションや精密機器なら静音性重視)に応じて、最適な歯型を選択する必要があるのです。
ただし、歯の強度やかみ合いの滑らかさには、次に説明する「圧力角」も大きく関わってきます。歯型と圧力角は、互いに関連し合いながら歯車の性能を決定づける要素なのです 。
注意点:歯型も一致が必要
モジュールと同様に、噛み合う歯車同士は、歯型も一致している必要があります。たとえモジュールが同じでも、並歯の歯車と高歯の歯車を無理に噛み合わせようとすると、正常に回転しなかったり、歯が干渉して破損したりする原因となります。歯車を選ぶ際や設計する際には、モジュールだけでなく、歯型も必ず確認するようにしましょう。
4. 力の伝わる角度:圧力角
モジュールで歯の大きさが決まり、歯型で高さのバランスが決まりました。次なる重要なパラメータは「圧力角(Pressure Angle, α)」です。これは、歯車同士が力を伝え合う際の「角度」に関わる要素です。
圧力角とは?
圧力角とは、簡単に言うと、歯車同士が接触して力を伝達する際に、その力が作用する方向と、歯車が回転する方向(ピッチ円の接線方向)とがなす角度のことです 。歯車の歯面上の接触点において、歯面に垂直な線(力が伝わる線)と、その点を通るピッチ円の接線との間の角度、とも定義されます 。
これをイメージするには、箱を押す場面を考えると良いかもしれません。箱を真横から水平に押せば、押した力は効率よく箱を動かす力になります。しかし、斜め上や斜め下から押すと、力の一部は箱を床に押し付けたり持ち上げたりする方向に逃げてしまい、横に動かす効率は落ちます。歯車における圧力角は、この「押す角度」に似た概念です。
もう少し技術的に見ると、現在主流のインボリュート歯車では、噛み合っている歯同士が力を伝え合う点は、常に一本の直線上を移動します。この直線を「作用線(Line of Action)」と呼びます 。作用線は、歯形(インボリュート曲線)を作り出す元になる二つの円、「基礎円(Base Circle)」の両方に接する線です 。そして、圧力角は、この作用線と、歯車中心を結ぶ線に垂直な線(ピッチ円の共通接線)とがなす角度として定義されます 。インボリュート歯車の場合、この圧力角は噛み合い中に変化せず一定です 。
なぜ圧力角が重要なのか?
この「力の伝わる角度」である圧力角は、歯車の性能に根本的な影響を与えます 。具体的には、以下のような点に関わってきます。
- 力の伝達効率 (Power Transmission Efficiency): 圧力角は、入力された力がどれだけ効率よく出力側の回転力に変換されるかに影響します 。
- 歯の強度 (Tooth Strength): 歯が曲げや折損にどれだけ耐えられるかは、圧力角によって大きく変わります 。
- 騒音・振動 (Noise/Vibration): 歯車がどれだけスムーズに、静かに回転するかにも圧力角が関係します 。
- 摩耗・寿命 (Wear/Durability): 歯面の接触状態や応力に関わるため、摩耗の進み具合や歯車の寿命に影響します 。
- アンダーカット (Undercutting): 歯数が少ない歯車を加工する際に、歯元がえぐれてしまう「アンダーカット」の発生しやすさに関係します。アンダーカットは歯の強度を著しく低下させます 。
- 全体的な品質 (Overall Quality): 設計通りの正確な圧力角で加工されていることが、高品質な歯車には不可欠です 。
これらの性能要素は独立しているわけではなく、互いに関連し合っています。例えば、圧力角を大きくすると、一般的に歯元が太くなり歯の曲げ強度は向上します 。また、アンダーカットも発生しにくくなります 。これらはメリットと言えます。しかしその一方で、圧力角が大きいと歯車同士を離そうとする力(スラスト力)が大きくなったり 5、接触時の衝撃や滑りが増えて騒音や振動が大きくなる傾向があります 。また、同時噛み合い歯数(かみ合い率)が減少し、滑らかさが低下することもあります 。
このように、圧力角の選択は、単一の性能を最大化するのではなく、複数の性能要因間のトレードオフを考慮し、使用される機械の目的や要求性能に合わせて最適なバランスを見つける作業なのです。強度を最優先するのか、静粛性を重視するのか、あるいは効率や寿命を最大化したいのか、その目的によって最適な圧力角は変わってきます。
標準的な圧力角:20°が主流
モジュールと同様に、圧力角も国際的に標準化されています 。これにより、互換性の確保や製造の効率化が図られています。現在、最も広く使われている標準圧力角は20°です。
- 20°: 現在の国際標準(ISO)であり、日本のJIS規格でも標準とされています 。強度、効率、静粛性、製造の容易さなどのバランスが良く、非常に多くの用途で採用されています 。
- 14.5°: かつて広く使われていた古い規格の圧力角です。一般的に20°よりも静粛性に優れるとされますが、歯の強度が低く、アンダーカットが発生しやすいという欠点があります 。現在では、新しい設計で採用されることは稀ですが、補修部品などで見かけることがあります。
- 25° (またはそれ以上): より高い強度や負荷容量が求められる、特殊な用途や重工業向けの歯車で使われることがあります 。強度面では有利ですが、騒音や振動、軸受への負荷が増加する可能性があります。
標準的な角度を使用することの重要性は、モジュールの場合と同様です。異なる圧力角の歯車同士を噛み合わせることはできません 。例えば、圧力角20°の歯車と14.5°の歯車は、たとえモジュールや歯数が同じでも、正しく噛み合わないのです。
かつて主流だった14.5°から20°へと標準が移行した背景には、技術の進歩と経済性のバランスがあります。20°は14.5°に比べて歯元が厚く強度が高いだけでなく、アンダーカットを起こしにくいため、より少ない歯数で小さな歯車(ピニオン)を設計できます 。これにより、機械全体の小型化や軽量化、より大きな減速比の実現が可能になります 。一方で、かつては14.5°の方が静粛性や摩耗の点で有利とされていましたが、材料技術や加工精度、潤滑技術の向上により、20°でも多くの用途で十分な静粛性や耐久性が得られるようになりました。結果として、強度や設計自由度の高さを優先した20°が、現代の多様な機械的要求に応えるための、優れた工学的妥協点として広く受け入れられたと考えられます。
圧力角が大きい vs 小さい (20° と 14.5° の比較を中心に)
ここで、代表的な標準圧力角である20°と、旧規格の14.5°の主な違いを比較してみましょう。
表2:圧力角 20° と 14.5° の比較
特徴 | 20° 圧力角 (現在の標準) | 14.5° 圧力角 (旧規格) |
歯の強度 | 高い (歯元が太い) 7 | 低い 5 |
静粛性・滑らかさ | やや劣る傾向 5 | 高い (滑らかなかみ合い) 5 |
アンダーカット | 起こりにくい (少ない歯数でも設計可) 5 | 起こりやすい (多くの歯数が必要) 5 |
負荷容量 | 高い 21 | 低い 5 |
主な用途 | 一般的な機械全般 | 旧式機械の補修、特殊用途 |
互換性 | 現在の主流規格 | 20°とは互換性なし 21 |
この表からわかるように、20°は強度や設計自由度(小型化、高減速比)に優れる一方、14.5°は静粛性が主な利点でした。現代の多くの機械設計では、20°の利点が総合的に評価され、標準として採用されています。
モジュールや歯型との関係
繰り返しになりますが、歯車が正しく機能するためには、モジュール、歯型、そして圧力角の3つすべてが、噛み合う相手の歯車と一致している必要があります。歯車を設計する際には、これらのパラメータを総合的に考慮し、目的の性能を達成するように選択します。
5. 微調整の鍵:転移量
最後に紹介するのが「転移量(てんいりょう、Profile Shift)」です。モジュールで基本的なサイズが決まり、歯型で大まかな性能特性(強度 vs 静音性)の方向性が決まり、圧力角で力の伝わり方やさらなる性能バランスが決まった後、さらに微調整を行うためのパラメータが転移量です。
転移量とは?
転移量とは、歯車を加工(歯切り)する際に、基準となる円(ピッチ円)に対して、歯切り工具の位置を意図的に半径方向にずらす(転移させる)量のことです。このずらす量を、通常はモジュールを基準とした係数(転移係数 x)で表し、実際の転移量は x×m (mm) となります。
想像してみてください。丸い生地から歯車の形を切り出すカッターがあるとします。通常は生地の中心とカッターの中心を合わせて切り抜きますが、転移は、このカッターを生地の中心から少し外側(プラス転移、+x)または内側(マイナス転移、−x)にずらして切り抜くようなイメージです。
工具の位置をずらすことで、出来上がる歯の形も微妙に変化します。
- プラス転移(工具を外側にずらす): 歯切り工具が外側に移動するため、歯の根元の削られる量が減り、逆に歯先の削られる量が増えます。結果として、歯先は細く(尖りやすく)なり、歯元は太くなります。
- マイナス転移(工具を内側にずらす): 工具が内側に移動するため、歯の根元がより深く削られ、歯先はあまり削られません。結果として、歯先は太く(平らっぽく)なり、歯元は細くなります。
なぜ転移を使うのか?
この微妙な形状変化を利用して、歯車の設計者は様々な問題を解決したり、性能を最適化したりします。転移が使われる主な理由は以下の通りです。
- アンダーカットの防止: 歯数が少ない歯車(小ギア、ピニオン)を標準的な方法(転移ゼロ)で加工すると、特に圧力角が低い場合(例:14.5°)や歯数が極端に少ない場合に、歯の根元部分が必要以上に深く削られてしまい、くびれたような形状になることがあります。これを「アンダーカット」と呼び、歯の強度を著しく低下させる原因となります。プラスの転移を行うことで、歯元が太くなり、アンダーカットを防ぐことができます。これは、転移が使われる最も一般的な理由の一つです。
- 中心距離の調整: 歯車を設計する際、理論的にはモジュールと歯数で決まる「標準中心距離」で噛み合わせますが、実際の機械設計では、スペースの制約や他の部品との兼ね合いで、標準とは少し異なる中心距離で歯車を配置したい場合があります。一方の歯車にプラス転移、もう一方にマイナス転移を施すことで標準中心距離を維持したり、両方にプラス転移を施して中心距離を広げたりするなど、歯車の中心距離をある程度自由に調整することが可能になります。
- 歯の強度バランスの最適化: プラス転移で歯元を太くして曲げ強度を向上させることができます。特に、歯数の少ないピニオンと歯数の多いギアが噛み合う場合、ピニオンの方が強度的に不利になりがちですが、ピニオンにプラス転移を施すことで強度を補強し、ギアとの強度バランスを取ることができます。
- かみ合いの改善: 特定の用途において、かみ合い始めや終わりの滑らかさを改善したり、バックラッシ(歯と歯の間の隙間)を調整したりする目的で使われることもあります。
このように、転移は、モジュール、歯型、圧力角で決まる基本的な設計の上に、さらに特定の課題解決や性能の微調整を行うための「応用技術」と言えます。基本的な互換性を決めるモジュールや圧力角、大まかな性能特性を決める歯型とは異なり、より専門的で、設計の自由度を高めるためのパラメータです。転移は、他のパラメータ選択によって生じる制約(例えば、少ない歯数や低い圧力角によるアンダーカットのリスク)を補正したり、特定の性能(強度や中心距離)をさらに追求したりするための強力な調整手段として機能します。
注意点
転移は便利な手法ですが、万能ではありません。過度な転移(特に大きなプラス転移)は、歯先が極端に尖ってしまい、強度不足や摩耗の原因になることがあります。また、転移させた歯車(転移歯車)と標準の歯車(転移ゼロ)を噛み合わせることも可能ですが、最適な性能を得るためには、噛み合う相手の歯車も適切に転移量を設定(例えば、一方をプラス転移、他方をマイナス転移するなどして、転移係数の和を調整する)することが一般的です。転移量の決定には、専門的な計算と経験に基づいた配慮が必要です。
6. おわりに
今回は、歯車の基本となる4つの重要な要素、「モジュール」、「歯型」、「圧力角」、「転移量」について解説しました。
- モジュール: 歯の大きさを決める世界共通の基準。同じモジュールなら基本、噛み合える可能性がある。標準化が互換性と製造効率を生む。
- 歯型: 歯の高さの比率を変え、強度(低歯)と静音性・滑らかさ(高歯)のバランスを調整する。モジュールによる比例スケーリングの限界を補う。
- 圧力角: 力が伝わる角度。強度、効率、騒音、摩耗、アンダーカット防止などの性能バランスを決定する重要な要素。20°が現在の主流。
- 転移量: 歯切り工具の位置をずらし、歯形を微調整。アンダーカット防止や中心距離調整、強度最適化など、特定の問題解決や性能最適化に使う応用技術。
これらの基本的な概念を理解することは、歯車がどのように機能し、どのように設計・選択されるのかを知るための第一歩です。重要なのは、これらのパラメータが独立しているのではなく、互いに影響し合いながら歯車の最終的な性能を決定しているということです。設計者は、機械の用途や要求される性能に応じて、これらのパラメータを最適に組み合わせる必要があります。
普段何気なく目にしている機械の中で、これらのパラメータがどのように活かされているのか想像してみると、より一層、機械の世界が面白く感じられるかもしれません。
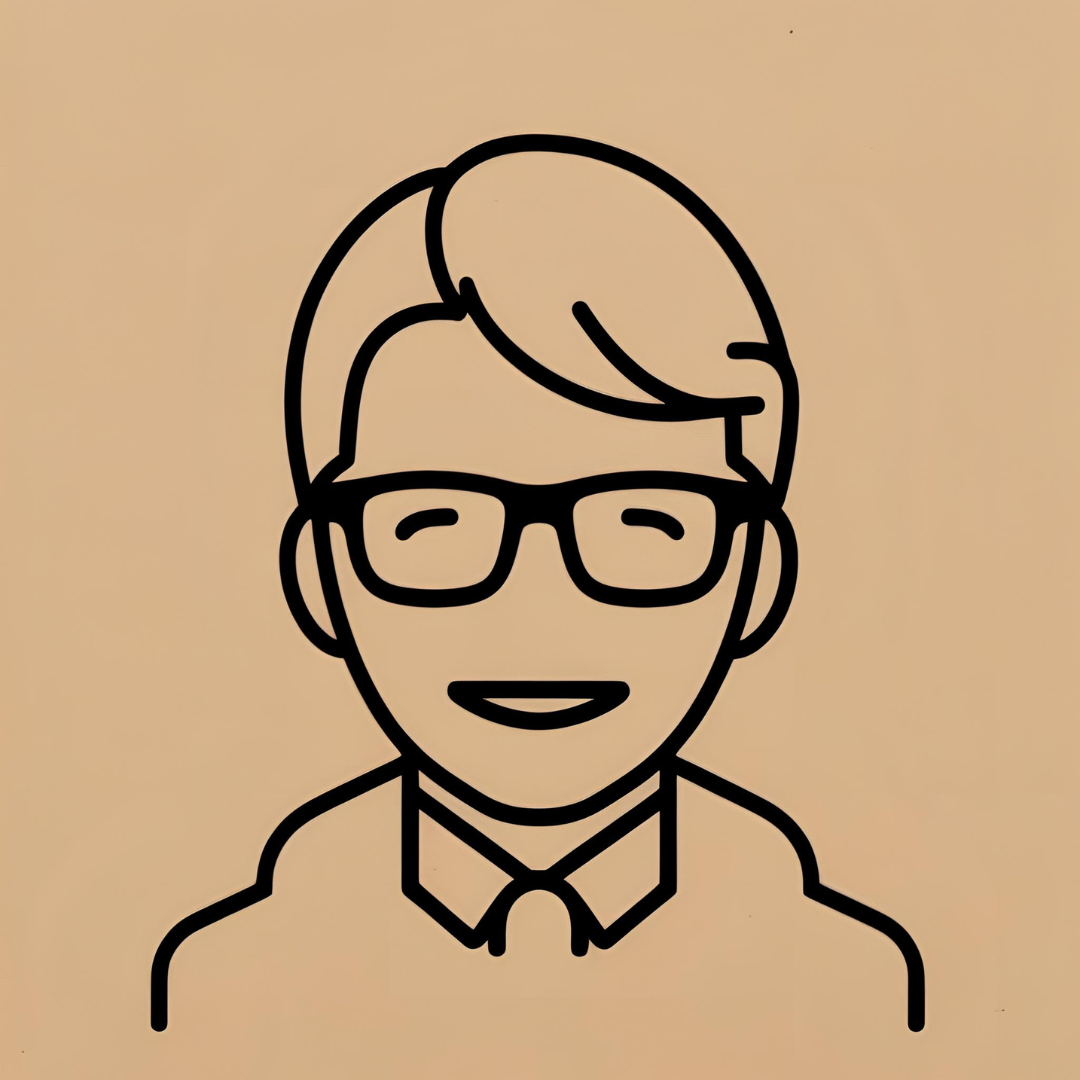
歯車の世界は奥深く、今回紹介した以外にも「はすば歯車」「かさ歯車」「ウォームギア」といった様々な種類の歯車や、「バックラッシ」「潤滑」「材料」など、さらに多くの要素が絡み合っています。
機会があれば紹介しますね