代表的なボルト4種類
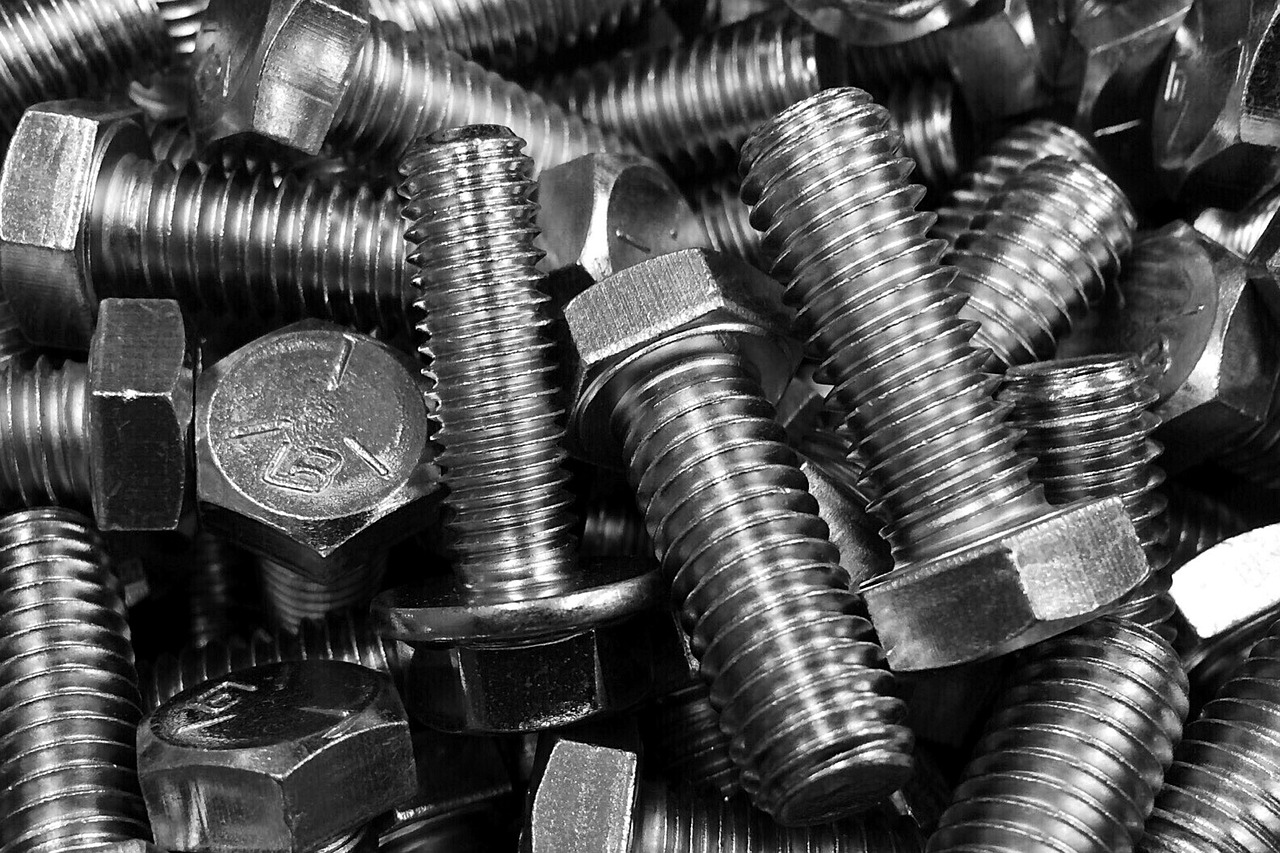
ボルトと一口に言っても、その種類はネジ部の規格、材質、長さ、そして頭部の形状など、多くの組み合わせによって非常に多岐にわたります。特に「頭の形状」は、使う工具や締め付けやすさ、適した用途に大きく関わってきます。
今回は、ボルトの頭の形状を「工具形状」という観点から分類し、代表的な4つのタイプについて、それぞれのメリット・デメリット、そしてどんな場面で使われることが多いのかを詳しく解説していきます。
ボルトの種類の基本:工具形状と座面形状
ボルトの種類は様々な要素の組み合わせで決まりますが、頭の形状は大きく「工具をかける部分の形状」と「座面(部材に接する面)の形状」で分類できます。この記事では、特に「工具をかける部分の形状」に焦点を当てて見ていきましょう。代表的なものとして、以下の形状があります。
- プラス(十字穴)
- 六角穴
- 六角(外六角)
- トルクス(ヘクサロビュラ)
それぞれ詳しく見ていきましょう。
1. プラスねじ(十字穴付きねじ)
私たちの生活で最も身近なねじの一つが、このプラスねじではないでしょうか。
- 使用工具: プラスドライバー
- メリット:
- ツールパス(工具の通り道)が狭くて済む: 工具の先端が細いため、狭い場所でも使いやすく、周辺部品に工具が接触して傷つけるリスクが低い。
- 入手性と手軽さ: プラスドライバーは広く普及しており、グリップが付いた持ちやすいものが多く、手軽に使えます。
- デメリット:
- 高いトルクを伝えにくい: 工具先端の径が小さく、力の作用点が回転中心に近いため、大きな力をかけるのが苦手です。
- カムアウトしやすい: 回転させると、ネジ穴の形状と工具の形状(先端に向けて細くなる)によって、工具が穴から浮き上がって外れやすい「カムアウト」という現象が起こります。これを防ぐには、ドライバーを強く押し付けながら回す必要があり、「押しが8割」と言われるほどです。
- なめやすい(頭を潰しやすい): カムアウトしやすいため、特に力の加減を誤るとネジの十字穴を潰してしまいやすいです。作業者のスキルに依存する面もあります。
- 主な用途:
- 精密機器: パソコン内部など、周辺部品への接触を避けたい、かつ大きな締め付けトルクが不要な箇所。
- 小ねじ: 大きなトルクが必要ない一般的な箇所。
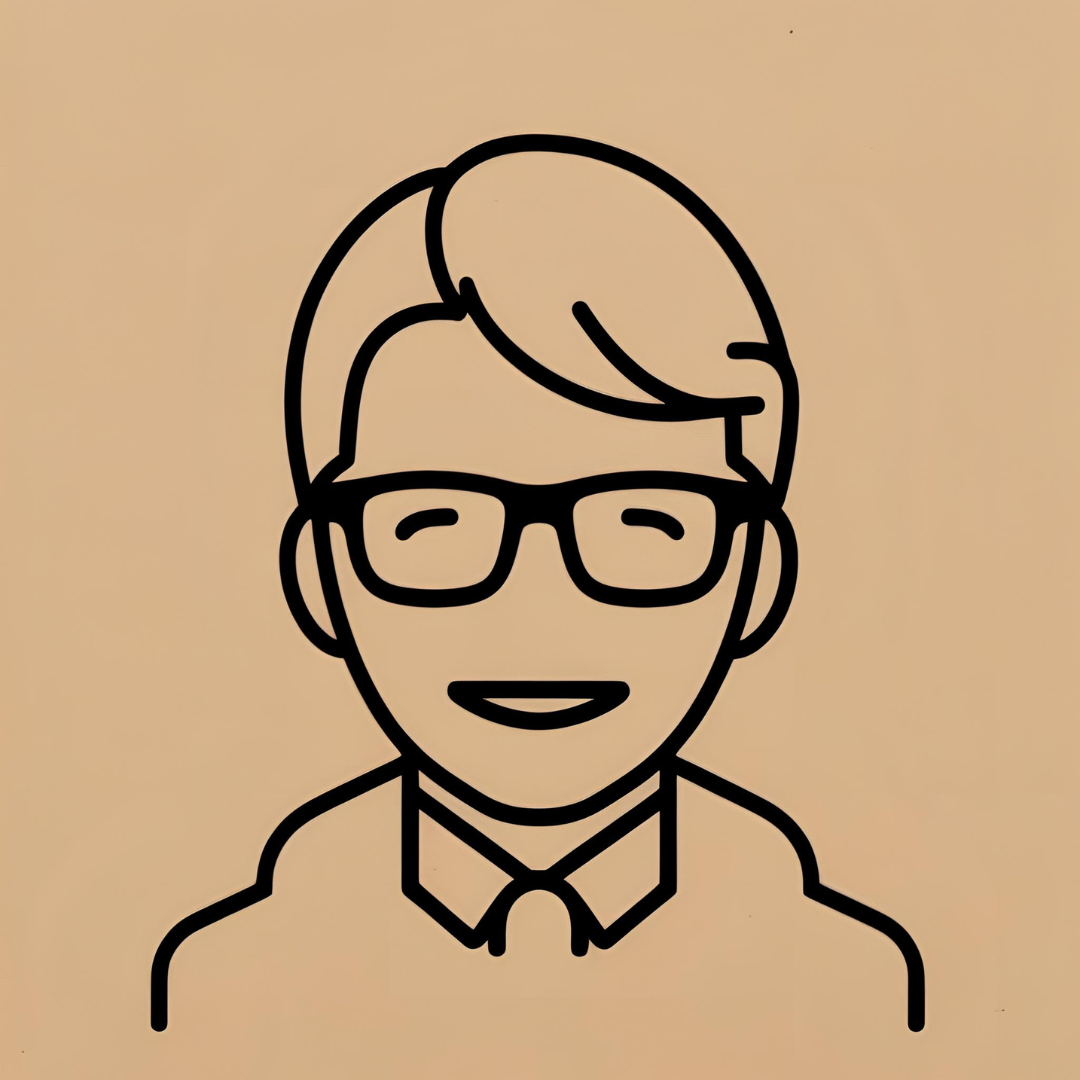
ツールが細いのはプラスねじの大きなアドバンテージなんだ。昔のバイクや車に使われていたキャブレターという部品は
・細かい作業が必要
・空気の入り口を誤って少しでも傷つけない
・分解組み立ての作業は熟練の作業者の仕事
という理由で、後述の六角ボルトは使わずプラスねじを好んで使っていたという説もあるよ。
2. 六角穴付きボルト(キャップボルト)
六角形の穴が空いているボルトです。キャップスクリューとも呼ばれます。
- 使用工具: 六角レンチ(ヘックスレンチ、アレンキー)
- メリット:
- 安定したトルク伝達: プラスねじよりも確実かつ安定してトルクを伝えることができます。
- カムアウトしにくい: 工具を穴の奥までしっかり差し込めば、カムアウト現象はほとんど起こりません。
- 省スペース: 後述の外六角ボルトに比べて、ボルトの頭部自体がコンパクトです。工具はL字型などになりますが、締め付け作業に必要なスペース(ツールパス)は外六角より小さくできます。
- デメリット:
- なめやすい(穴を潰しやすい): 外六角ボルトに比べると力の作用点が中心に近く、穴の角に力が集中しやすいため、特に強いトルクをかけると穴をなめてしまう(潰してしまう)ことがあります。
- 工具が破損しやすい: 高トルクをかける場合、工具(レンチ)の軸径が比較的細いため、工具側がねじれたり折れたりすることがあります。
- ボルト強度が必要: 締め付け時に穴をなめないように、ある程度のボルト強度(例: 強度区分8.8や10.9など)が求められます。
- 主な用途:
- 機械内部: 省スペースで、かつプラスねじよりもしっかり締め付けたい箇所。
- 組み立て家具: 適度な締め付けトルクが得られ、工具(六角レンチ)が安価で付属させやすいため、よく利用されています。
- デザイン性: ボルトの頭を部材に埋め込む(ザグリ加工)ことで、表面をフラットに仕上げたい場合など。
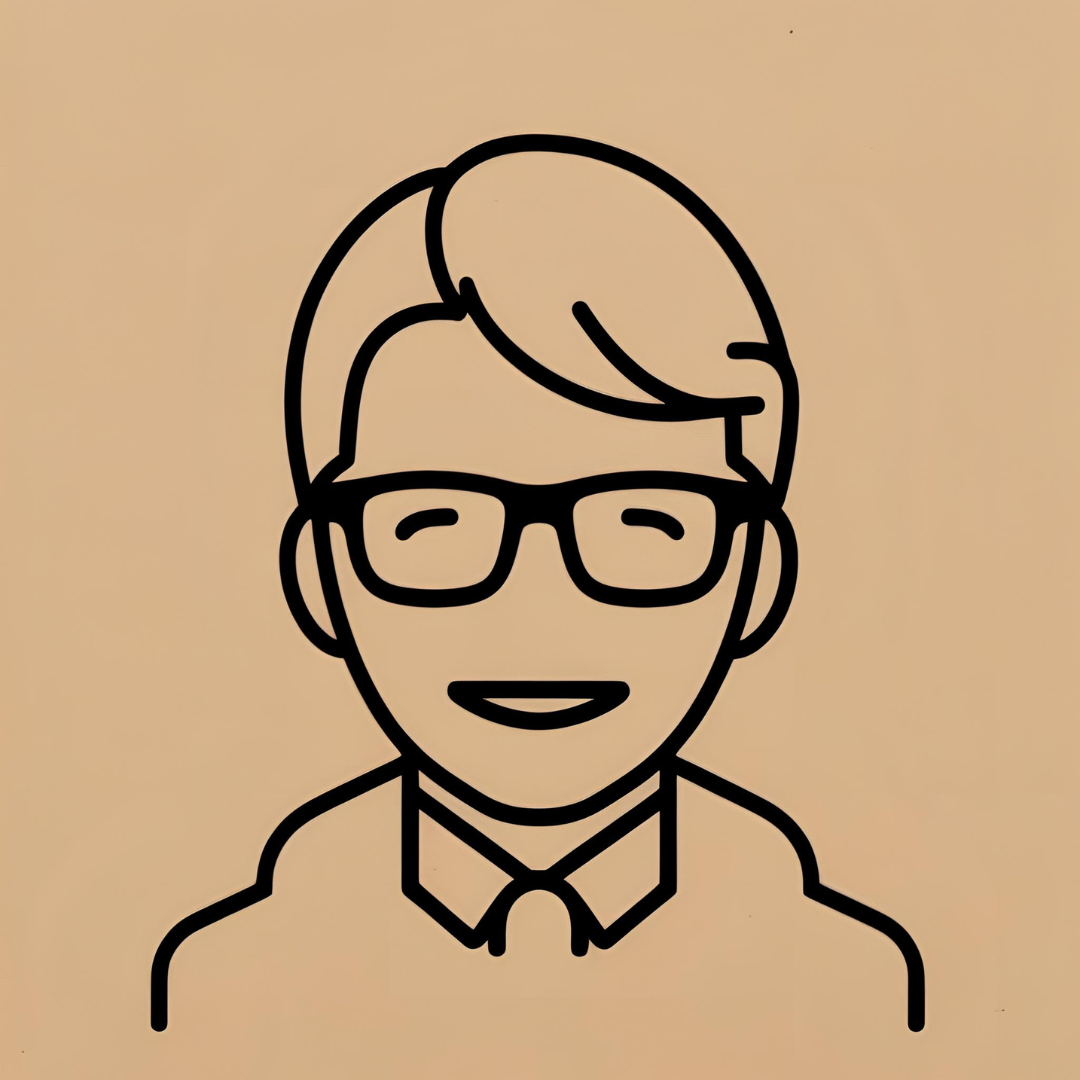
内六角ボルトの締め付けには、ボールポイントという斜めからでも締め付けられるツールがあります。でも、斜めから締め付けるので
・かみ合い始めから使うと、ボルトが斜めに噛んでしまってねじ山をつぶしてしまう
・規定トルクで締め付けても、斜めの分力しか伝わらないので、トルク管理が難しい。
という難点もあるので、出来るだけ使わないようにした方が安全ですね!
3. 六角ボルト(外六角ボルト)
ボルト頭の外周が六角形になっている、最も一般的なボルトの一つです。
- 使用工具: スパナ、メガネレンチ、ソケットレンチ、モンキーレンチなど多種多様。
- メリット:
- 最も高トルクに適している: 工具をかける部分が回転中心から最も遠いため、力の作用点にかかる負荷が少なく、非常に高いトルクで安定して締め付けることができます。なめにくいのも特徴です。
- 工具の選択肢が多い: 様々な工具が使用できるため、作業状況に合わせて最適な工具を選べます。
- トルク管理が容易: トルクレンチを使った精密なトルク管理にも適しています。
- 高い信頼性: 確実な締結ができるため、幅広い分野で使用されています。
- デメリット:
- 広い作業スペースが必要: ボルト頭部も工具も大きくなるため、締め付け作業にはある程度のスペース(ツールパス)が必要です。
- 主な用途:
- 自動車、バイク、鉄道車両: 高い締結力と信頼性が求められる箇所。
- 建設機械、産業機械: 強力な締結が必要なあらゆる箇所。
- 建築、橋梁、鉄塔: 構造物の接合部など、極めて高い信頼性が要求される箇所。
- 小ねじから大径ボルトまで、サイズを問わず幅広く使用されます。
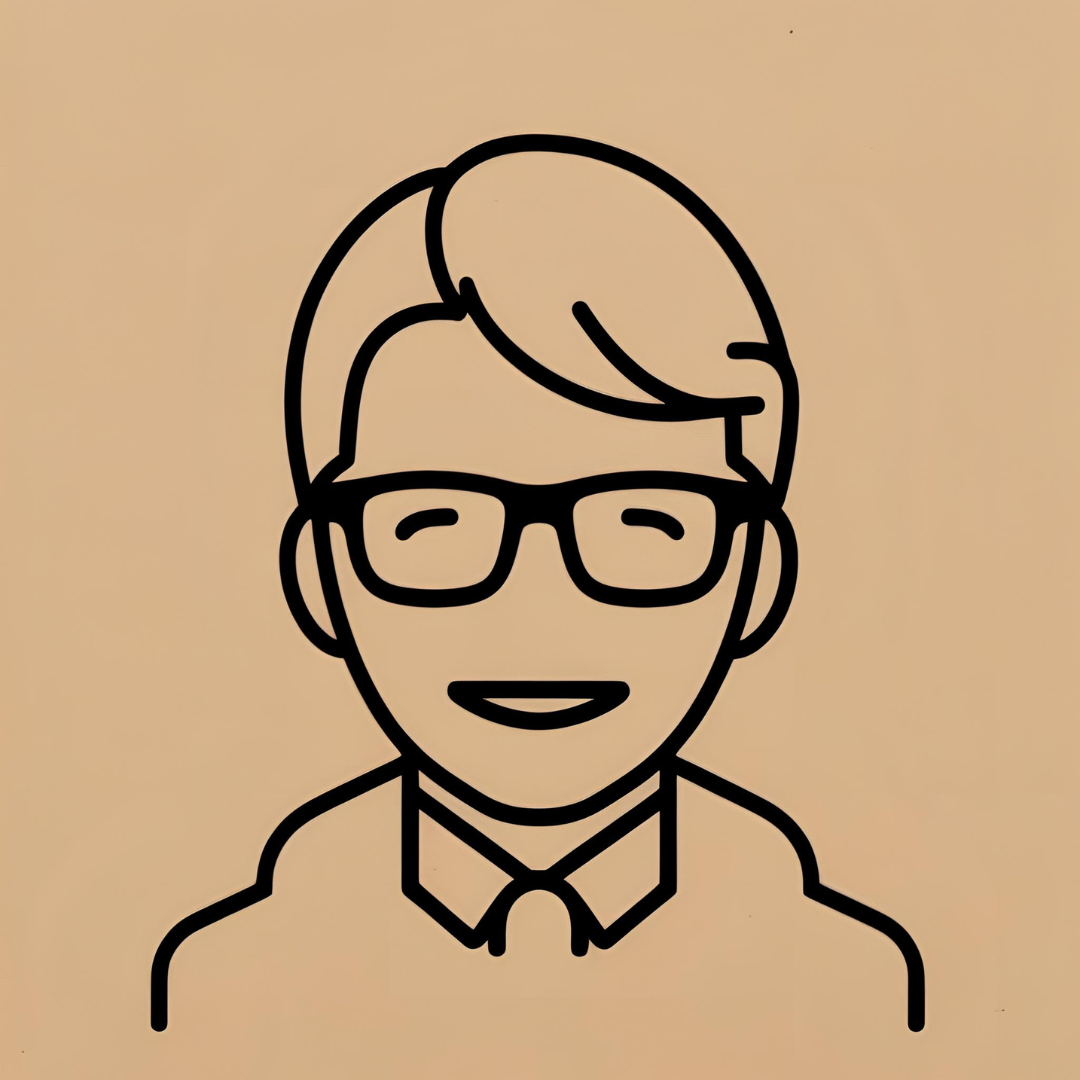
ボルト締め付けを軸力計算してまともに設計しようとすると、外六角ボルトか後述のトルクスを使いたくなります。
軸力計算するという事は、ある程度大きい外力が入り、締結の信頼性が重要な箇所という事。とすると、大トルクで締め付けられる外六角かトルクスを使わないと心配になっちゃうんです。
4. トルクス(ヘクサロビュラ)
比較的新しい規格で、星形のような形状をしています。(トルクスは登録商標で、一般名称はヘクサロビュラやヘクスローブとも呼ばれますが、現場ではトルクスで通じることが多いです)
- 使用工具: トルクスレンチ(内側にかけるT型と、外側にかけるE型があります)
- メリット:
- 非常になめにくい: 六角形が「線(角)」で接触するのに対し、トルクスは丸みを帯びた「面」で接触するため、力が分散し、非常に滑りにくく(なめにくく)、効率的にトルクを伝達できます。六角よりも高いトルクに耐えられます。
- カムアウトしにくい: 構造上、カムアウトもほとんど発生しません。
- デメリット:
- 専用工具が必要: トルクス用のレンチが必要です。
- 日本では普及率が低い: 後述の理由により、六角形ほど一般的ではありません。
- 主な用途・普及状況:
- 欧米の自動車: 特にヨーロッパ車などで多く採用されています。
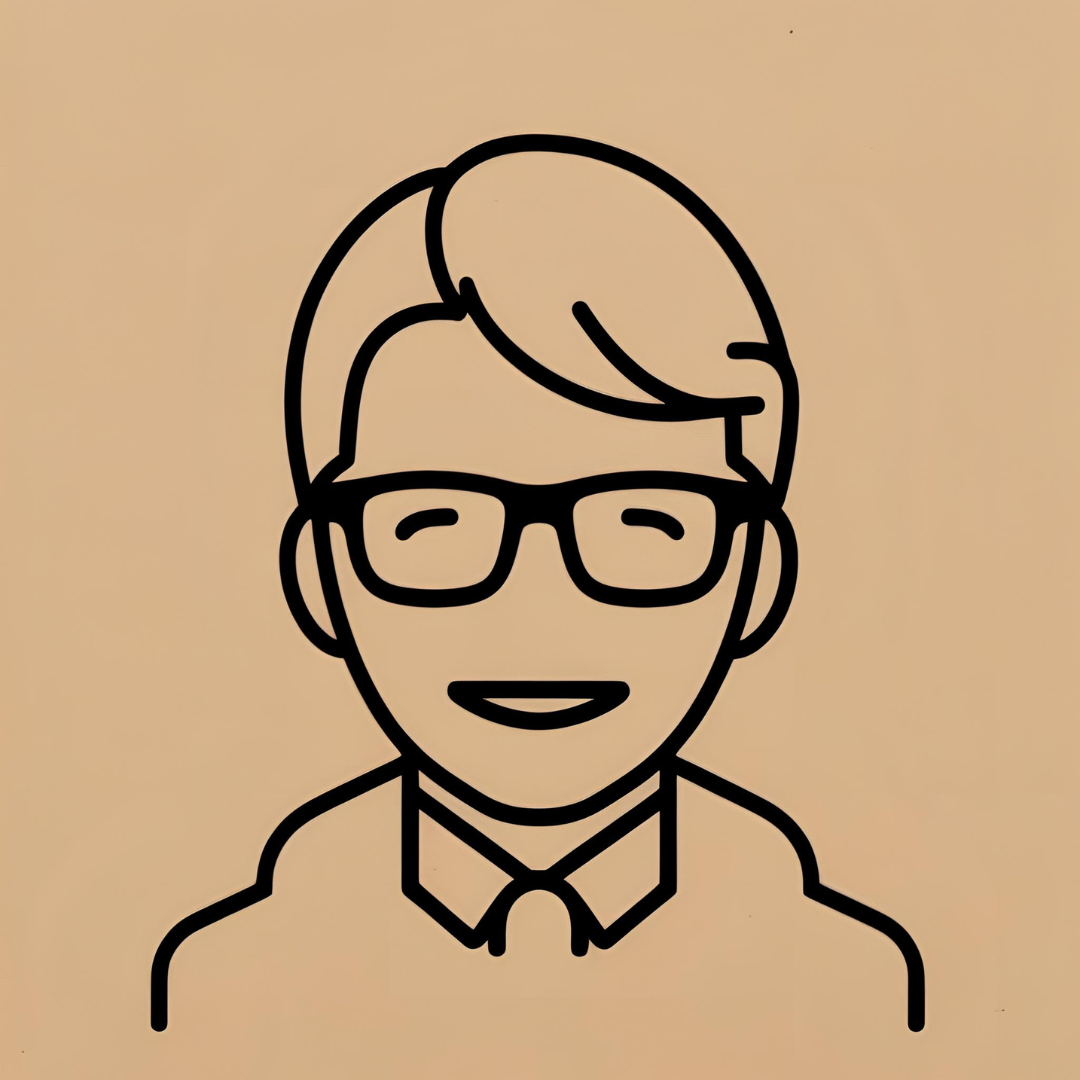
なぜ日本では少ないのか?
筆者の考えでは、日本の工業製品、特にボルトやナット自体の品質が高いことが一因と考えられます。高品質な六角ボルト・ナットは、適切な工具と作業方法であれば、トルクスでなくとも十分なトルクで締結でき、なめるリスクが比較的低いのです。(経験上、内六角ボルトをなめる前に工具の方が折損することが多いです。)そのため、既に広く普及し、多くの人が持っている六角用の工具が使える利便性が優先され、日本では六角穴付きボルトや六角ボルトが主流であり続けていると考えられます。
まとめ
今回は、ボルトの頭の形状を「工具をかける部分」に注目して4種類ご紹介しました。
種類 | トルク伝達 | なめにくさ | 省スペース性 | 工具の汎用性 | 主な用途例 |
---|---|---|---|---|---|
プラス | △ | △ | ◎ | ◎ | 精密機器、小ねじ、低トルク箇所 |
六角穴 | 〇 | 〇 | 〇 | △ | 機械内部、家具、中トルク箇所、省スペース |
外六角 | ◎ | ◎ | △ | ◎ | 自動車、建築、高トルク箇所、高い信頼性が必要な箇所 |
トルクス | ◎ | ◎ | 〇 | × | 欧米車、特殊用途、高トルク伝達 |
(◎:非常に良い、〇:良い、△:やや劣る、×:劣る)
今回は紹介しませんでしたが、ユーザーが勝手にボルトを緩めないように、締め付け方向しか力が加わらない穴形状、盗難/いたずら防止のための特殊な穴形状など、様々な形があります。
どのボルトを選ぶかは、必要な締め付けトルクの大きさ、作業スペースの広さ、求められる信頼性や精度や機能、そしてコストなどを総合的に判断して決めることが重要です。
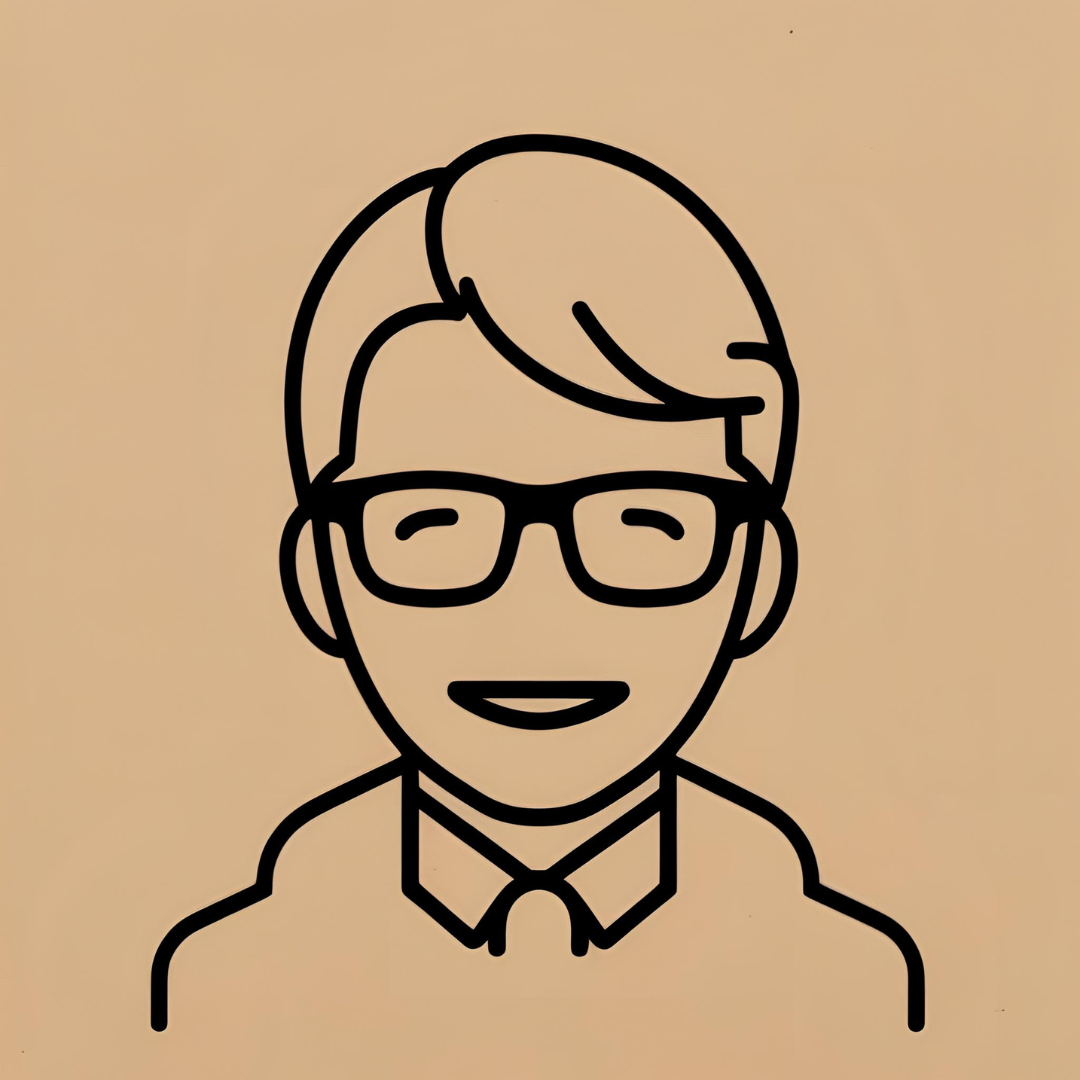
どの形状ボルトが安いかは一概には言えません。
表面処理や精度などのスペックに加えてボルトメーカーの得意/不得意もありますが、それ以上に流通性が大きな要素となります。
似たボルトでも流通性で単価の桁が一つ変わることも多いので、設計者はその点も事前確認をしましょう。